Автоматизация системы ТОИР на двигателестроительном предприятии ПАО «ОДК-УМПО»
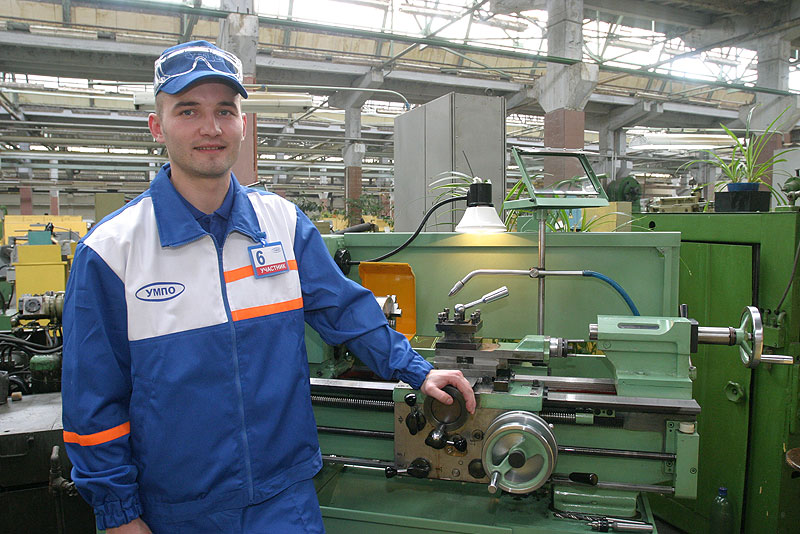
Заказчик:
ПАО «ОДК-Уфимское моторостроительное производственное объединение»
О компании:
ПАО «ОДК-Уфимское моторостроительное производственное объединение» – разработчик и крупнейший производитель газотурбинных двигателей в России.
Основными видами деятельности являются разработка, производство, сервисное обслуживание и ремонт турбореактивных авиационных двигателей, производство и ремонт узлов вертолетной техники, выпуск оборудования для нефтегазовой промышленности.
В объединении работают более 24 000 человек.
:
Автоматизация технического обслуживания и ремонта оборудования
Решение:
реализация:
Паспортизация оборудования, ведение нормативов
В системе ведется учет всего парка оборудования, имеющегося на предприятии. От производственных станков до вентиляционного и подъемного оборудования.
Результат:
За 3 месяца в системе из разных источников была аккумулирована информация по 19 тысячам единиц оборудования, из них это 12 тысяч станков с количеством моделей 4,5 тысячи
Управление технической документацией
Техническая документация на станки хранится в электронном архиве системы в структурированном виде:
- Паспорт;
- Руководство по эксплуатации;
- Электрическая часть;
- Механическая часть;
- Спецификация по запчастям;
- Копия программы ЧПУ на электронном носителе;
- Система управления ЧПУ.
Документация загружается в систему с обязательным указанием вида и модели станка к которому относится.
Электронный поиск по заданным реквизитам позволяет быстро найти нужную документацию в системе.
Результат:
До момента внедрения системы документация по станкам не хранилась централизовано. Электронная документация в виде файлов разного формата хранилась на компьютерах специалистов в цехах.
На данный момент идет процесс инвентаризации документации и ее структурированного внесения в электронный архив. В систему загружена документация на 800 моделей станков
График планово-предупредительных ремонтов
В системе заложены алгоритмы формирования графиков ППР, построенные на основании типовых схем ТОИР, рекомендуемых в машиностроительной отрасли для различных видов оборудования.
Определение КР и СР по типовым схемам часто бывают избыточны и техническое состояние оборудования позволяет выполнять их менее регулярно. Поэтому для оценки технического состояния оборудования, собираются экспертные заявки на проведение среднего и капитального ремонтов в следующем году от механиков цехов.
На основании этих заявок система по заложенным алгоритмам комбинирует график ППР рассчитанный по типовой схеме и на основании заявок от механиков
На основании годового план-графика ППР система формирует план-задание на следующий месяц. На основании фактической наработки за прошедшие месяцы в план-задание вносится корректировка сроков проведения ремонта, либо его отмена в этом месяце.
Сформированное план-задание отправляется в систему электронного документооборота на согласование. И в системе отслеживаются статусы согласования.
На станках с ЧПУ установлены счетчики моточасов, показания по которым ежемесячно вносятся в систему. Информация по наработке моточасов используется для построения графика ППР и анализа простоя станков.
Учет проведенных ремонтов
Информация о всех выполняемых работах с оборудованием отражается в документе Ремонт.
Не закрытые ремонты выделены в реестре красным цветом.
В документе «Ремонт» фиксируются :
- Документ-основание для ремонта (для внеплановых ремонтов – Журнал вызовов, для плановых ремонтов – План-задание);
- Замечания и требования цеха-заказчика;
- Плановый и фактический объем работ (трудозатраты);
- Плановое и фактическое время простоя оборудования;
- Плановые и выполненные работы в разрезе деталей и сборочных единиц;
- Плановые и фактически израсходованные запасные части для каждой выполняемой работы при ремонте;
- Дефекты обнаруженные при ремонте (выбор из классификатора дефектов);
- Специалисты, сдавшие и принявшие в ремонт;
- Печатаются Акт передачи в ремонт и Акт приемки из ремонта; Ведомость содержания работ; Карта точности с фактическим данными и др.
- Фиксируются данные проверки на точность.
Учет внеплановых ремонтов
При возникновении ситуации, требующей внепланового ремонта в цехе формируется заявка в Журнал вызовов (отражаются все ситуации от перегоревшей лампочки до серьезных аварий).
Проверка оборудования на технологическую точность
Оборудование должно проходить проверки на технологическую точность. В справочниках системы регистрируются карты точности для каждой модели станка, в которой указываются параметры и нормативные допуски к ним.
Для плановых проверок формируется годовой план-график проверок, в котором указывается оборудование, набор проверяемых параметров и плановый месяц проверки. После среднего и капитального ремонтов, оборудование должно проходить проверку на точность по всем параметрам.
Функциональный состав:
- Регистрация справочной информации по оборудованию: проверяемый параметр, метод проверки (графическое изображение), допуск, мм
- Формирование план-графика проверок на точность на год в разрезе месяцев
- Формирование Актов по результатам проверки оборудования на точность (регистрация в системе и печать регламентированных форм)
Результат:
В системе регистрируются все факты проверки и указываются фактические отклонения параметров.
Учет простоя оборудования
В системе заложены алгоритмы для определения плановых нормочасов простоя оборудования в разрезе видов ремонта. Алгоритм зависит от группы ремонтной сложности, определяемой в справочнике моделей и оборудования.
Плановые нормочасы простоя оборудования показываются в документе ремонт. В этом же документе фиксируется фактическое время простоя оборудования во время ремонта
Результат:
Система позволяет анализировать плановое и фактическое время простоя оборудования, выяснять причины простоя.
Планирование и учет затрат на материалы и запасные части
В системе заложены 2 алгоритма получения перечня ТМЦ, необходимых для ремонта и эксплуатации оборудования на следующий год.
1 схема:Формирование заявок на потребность ТМЦ механиками цехов на следующий год (указывается необходимое количество и технические характеристики ТМЦ). Заявки консолидируются в сводную заявку. Анализируется наличие остатков ТМЦ на складах и заявки с необходимым количеством для закупа согласуются через СЭД.
2 схема:Автоматическое формирование заявок в системе на основании графика ППР и ведомости содержания работ, в которой указываются необходимый перечень ТМЦ для выполнения работ по графику ППР
Результат:
Сопоставление данных о потребности в ТМЦ по результатам двух схем позволяют найти оптимальную потребность для закупа ТМЦ.
Эффекты:
1. Сокращение простоев оборудования и устранение «узких» мест в производственной цепочке благодаря:
- более надежной процедуре планирования запчастей
- для наиболее значимых станков формируется и автоматически поддерживается аварийный запас запчастей
- сокращению времени ремонта за счет быстрого оповещения, быстрого поиска документации
- минимизации ошибок в организации процесса ремонтов
2. Сокращение избыточных складских запасов благодаря:
- планированию закупок с учетом кратности заказа узлов
- автоматической проверке остатков на складах при оформлении заявки на закуп
- регламентированию времени заказа
- приоритетному использованию неликвидов